Profil użytkownika

matix
Kierowca
Zamieszcza materiały od: | 9 lutego 2012 - 20:59 |
Ostatnio: | 4 października 2016 - 20:08 |
- Materiałów na głównej: 47 z 48 (1 usunietych przez adm.)
- Punktów za materiały: 3027
- Komentarzy: 351
- Punktów za komentarze: 378

Przejdźmy do funkcji i budowy samego urządzenia. Gaźnik to urządzenie wytwarzające mieszankę paliwowo-powietrzną w odpowiednich proporcjach, potrzebną do prawidłowego spalenia w cylindrach.
Jego działanie opiera się na prawie Bernoulliego. Bez przytaczania zawiłych formułek naukowych, chodzi tu o zmniejszenie ciśnienia przepływającego powietrza w tzw. zwężce Venturiego. Przez gardziel gaźnika(2) silnik zasysa powietrze(1), przelatuje ono przez zwężkę i zmniejszając swoje ciśnienie „wysysa” paliwo z dyszy(6). Prędkość przelatującej mieszanki regulowana jest przez przepustnicę(7), która połączona jest z pedałem przyspieszenia. Za utrzymanie możliwie jak najbardziej stałych proporcji mieszanki odpowiada pływak(4) razem z zaworem iglicowym(5), który utrzymuje paliwo zawsze na tym samym poziomie, zawsze poniżej wylotu dyszy paliwowej, aby nie zalewać silnika. Pływak i zawór tworzą tzw. komorę pływakową(3).
Przedstawiony schemat to maksymalnie uproszczona wersja gaźnika, nie używana w praktyce(jak podaje Wikipedia – gaźnik elementarny).
Najczęściej spotykanymi usprawnieniami gaźnika są:
-studzienka emulsyjna
-urządzenie biegu jałowego;
-urządzenie rozruchowe.
Studzienka emulsyjna to drugi element po komorze pływakowej w drodze do dyszy paliwa. Znajduje się w niej rurka emulsyjna ze ściśle określoną liczbą dziurek. Rurka ta ma za zadanie wstępnie mieszać powietrze z paliwem. Jeden jej koniec wystaje na zewnątrz gaźnika aby można było dokonywać regulacji co do składu procentowego mieszanki.
Urządzenie biegu jałowego pozwala utrzymać motor na niskich obrotach podczas gdy kierowca nie naciska na pedał gazu, a co za tym idzie, gdy przepustnica jest całkowicie zamknięta. Jedynie przy ściankach gardzieli pozostaje mała szczelina dla przepływu powietrza, lecz paliwo podawane z głównej dyszy paliwa jest niewystarczające. Dlatego montuje się dodatkowy wylot paliwa na wysokości zamkniętej przepustnicy dla utrzymania silnika na biegu jałowym.
Urządzenie rozruchowe czyli tzw. ssanie. Wzbogaca ono mieszankę podczas uruchamiania silnika gdy prędkość obrotowa silnika nie jest wystarczają do zassania odpowiedniej jej ilości. W starszych gaźnikach jest ręcznie uruchamiane, ale w nowszych można spotkać sterowanie elektroniczne w zależności od temperatury silnika.
Istnieje wiele innych usprawnień układu, ale nie widzę sensu wymieniania ich wszystkich. W końcu ma być w miarę przejrzyście i prosto ;)
Wspomnę jeszcze o rozwiązaniach konstrukcyjnych, w zależności od kierunku przepływu powietrza:
-bocznossące(1) – gardziel ułożona poziomo, spotykane w motocyklach;
-górnossące(2) – stosowane przy silnikach dolno zaworowych, pionowy przelot w górę;
-dolnossące(3) – najczęściej spotykany, pionowo ułożona gardziel, kierunek przepływu w dół.
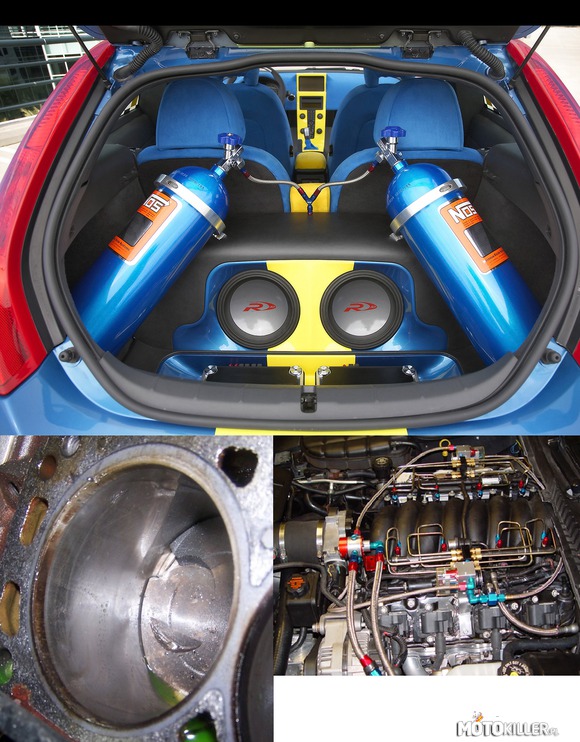
Dawkowanie N2O odbywa się skokowo, tzw. strzałem, gdyż ciągłe działanie tegoż gazu mogło by poważnie uszkodzić silnik. Istnieją trzy rodzaje instalacji nitro:
-dolot suchy – to wtrysk gazu do kolektora dolotowego. Jest to najsłabsza opcja dająca maksymalnie 15% przyrostu mocy;
-mokry – „podpięcie” się z dolotem podtlenku do przewodów paliwowych. Skok ok. 35%;
-bezpośredni – jest to najskuteczniejszy, ale i najbardziej inwazyjny oraz najdroższy sposób. N2O jest tutaj wtryskiwane bezpośrednio do cylindra.
Przed założeniem instalacji zaleca się gruntowne sprawdzenie silnika, ponieważ jednostki w słabym stanie mogą nie wytrzymać takich przeróbek. Szczególnie ważnym aspektem jest dobry stan uszczelki pod głowicą, gdyż ona musi wytrzymać ciśnienie wtłaczanego podtlenku.
Teraz trochę o samym działaniu tego gazu. Jak już pewnie wiecie silnik do spalania paliwa potrzebuje powietrza, ściślej – tlenu. W wysokiej temperaturze N2O rozkłada się na tlen i azot:
(2 N2O → 2 N2 + O2).
Większa ilość tlenu w komorze pozwala na spalenie większej ilości paliwa(idea ta sama co przy turbo). Dodatkowo azot schładza powietrze, które zmniejsza swoją objętość(analogia do intercoolera).
Jak możecie zobaczyć na zdjęciu właściciele takowych instalacji często instalują butle w widocznych miejscach aby stały się częścią wystroju auta. Poniżej, z lewej widać zbyt intensywnie „potraktowany” nitrem tłok, a obok przykład instalacji w silniku Corvette.
Na koniec zacytuję Wam fragment, który obrazuje jak rozpowszechniony jest ten wynalazek w USA: „System nitro jest tam tak popularny, jak gaz LPG w Polsce”. Warto tutaj zauważyć, że nitro nie tylko zwiększa moc ale mogłoby również oszczędzać paliwo gdyby nie fakt, że podczas używania dopalacza przepustnica powinna być maksymalnie otwarta. Być może przy zmodyfikowanej instalacji, przy mniejszych dawkach gazu można by rzeczywiście używać go do redukowania zużycia paliwa. Ale to tylko takie moje rozważania…

Przekrój turbosprężarki VGT przedstawiono na rysunku. Rolę kierownic strumienia spalin pełnią ruchome łopatki, a ich kąt nachylenia zmienia się poprzez kątowy obrót ruchomego pierścienia, na którym są osadzone łopatki. Spaliny dostają się kanałem (1) na łopatki turbiny. Podciśnienie w kolektorze ssącym (wytwarzane przez sprężarkę) działa na membranę siłownika¹ (9). Poprzez cięgno (4) zostaje obrócony pierścień sterujący (6), który zmienia kąt ustawienia łopatek (8) kierujących strugę spalin na turbinę (2). Położenie łopatek kierujących jest zależne od ciśnienia doładowania. Podczas pracy silnika z małą prędkością obrotową, łopatki zostają ustawione w położeniu zmniejszającym przekrój przepływu powietrza, które płynąc prędzej rozpędza turbinę do większej prędkości (rys. 1a i 2b). Dzięki temu silnik osiąga większą moc już w dolnym zakresie jego prędkości obrotowej. Gdy silnik pracuje z dużą prędkością obrotową, ciśnienie doładowania nie może być przekroczone i dlatego łopatki zostają ustawione w położeniu zwiększającym średnicę przekroju (rys. 1b i 2a). Przekrój przepływu jest na tyle zwiększony, aby przepływające powietrze napędzało koło turbiny tylko do wymaganej prędkości.
Istnieją również turbosprężarki VGT, w których zamiast regulowanych łopatek kierownicy stosuje się pierścień przesuwny, przysłaniający wlot spalin na łopatki kierownicy.
Pierwsze próby ze sprężarką VGT podjęła Honda w 1980 r. w modelu Legend Wing Turbo. Jednak pierwszym samochodem wyposażonym w turbosprężarkę VNT-25 Garret i skierowanym w 1989 r. do produkcji seryjnej (powstało tylko 500 egzemplarzy) był Shelby CSX-VNT z silnikiem 2.2L Chryslera. W Europie turbosprężarka o zmiennej geometrii pojawiła się po raz pierwszy w 1992 r. w modelu Peugeot 405 T16 z silnikiem 2.0 16V, który został wypuszczony w liczbie 1046 egzemplarzy. Swoją popularność turbosprężarki VTG zawdzięczają silnikom TDI koncernu VW, gdzie zaczęto je stosować od 1996 r. Chociaż technologia VTG jest już powszechnie stosowana w silnikach wysokoprężnych, to była ignorowana w silnikach benzynowych. Wynikało to z tego, że spaliny silników benzynowych mogą osiągnąć temperatury do 950°C w porównaniu do 700-800°C panujących w silnikach Diesla. A to sprawiało trudności w doborze materiałów na łopatki turbiny i w zachowaniu odpowiednich tolerancji, zwłaszcza w odniesieniu do ruchomych elementów. Konstruktorom udało się uporać z tym problemem dopiero w 2006 r. w silniku Porsche 911 (997) Turbo, dzięki metodom obliczeniowym i materiałom przejętym z lotnictwa. Dokładny skład tych ostatnich pozostaje tajemnicą firmy, wiadomo jednak, że na łopatki kierownicy użyto m.in. odpornego na wysokie temperatury stopu niklu.
Ponadto, z uwagi na większą ilość ruchomych elementów, turbosprężarki te są bardziej wrażliwe na zanieczyszczony(stary) olej a przy okazji remontu/wymiany bardziej kosztowne.
¹ - w nowszych układach stosuje się silniki krokowe sterowane komputerem co daje większą precyzję w regulacji obrotów turbo. Przykład na obrazku gdzie widać turbinę zastosowaną w silniku Audi 3.0 V6 TDI.
‹ pierwsza < 1 2 3 4 5 6 7 > ostatnia ›