Szukaj
Znalazłem 66 takich materiałów
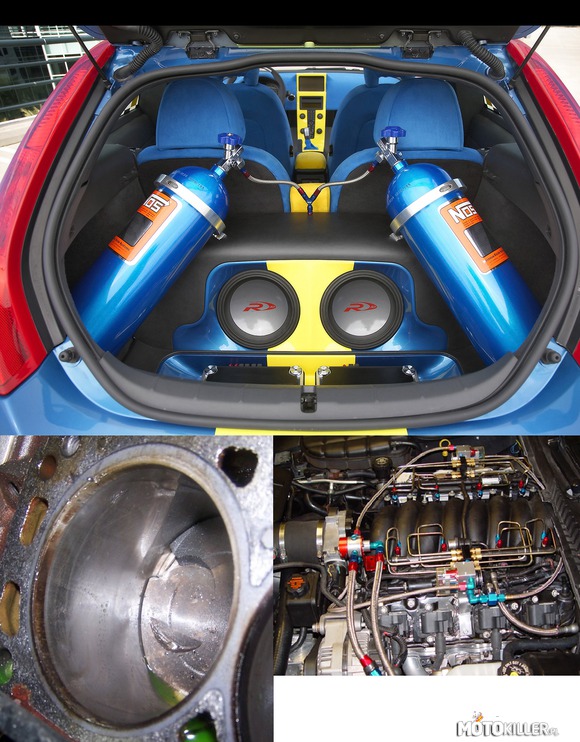
Dawkowanie N2O odbywa się skokowo, tzw. strzałem, gdyż ciągłe działanie tegoż gazu mogło by poważnie uszkodzić silnik. Istnieją trzy rodzaje instalacji nitro:
-dolot suchy – to wtrysk gazu do kolektora dolotowego. Jest to najsłabsza opcja dająca maksymalnie 15% przyrostu mocy;
-mokry – „podpięcie” się z dolotem podtlenku do przewodów paliwowych. Skok ok. 35%;
-bezpośredni – jest to najskuteczniejszy, ale i najbardziej inwazyjny oraz najdroższy sposób. N2O jest tutaj wtryskiwane bezpośrednio do cylindra.
Przed założeniem instalacji zaleca się gruntowne sprawdzenie silnika, ponieważ jednostki w słabym stanie mogą nie wytrzymać takich przeróbek. Szczególnie ważnym aspektem jest dobry stan uszczelki pod głowicą, gdyż ona musi wytrzymać ciśnienie wtłaczanego podtlenku.
Teraz trochę o samym działaniu tego gazu. Jak już pewnie wiecie silnik do spalania paliwa potrzebuje powietrza, ściślej – tlenu. W wysokiej temperaturze N2O rozkłada się na tlen i azot:
(2 N2O → 2 N2 + O2).
Większa ilość tlenu w komorze pozwala na spalenie większej ilości paliwa(idea ta sama co przy turbo). Dodatkowo azot schładza powietrze, które zmniejsza swoją objętość(analogia do intercoolera).
Jak możecie zobaczyć na zdjęciu właściciele takowych instalacji często instalują butle w widocznych miejscach aby stały się częścią wystroju auta. Poniżej, z lewej widać zbyt intensywnie „potraktowany” nitrem tłok, a obok przykład instalacji w silniku Corvette.
Na koniec zacytuję Wam fragment, który obrazuje jak rozpowszechniony jest ten wynalazek w USA: „System nitro jest tam tak popularny, jak gaz LPG w Polsce”. Warto tutaj zauważyć, że nitro nie tylko zwiększa moc ale mogłoby również oszczędzać paliwo gdyby nie fakt, że podczas używania dopalacza przepustnica powinna być maksymalnie otwarta. Być może przy zmodyfikowanej instalacji, przy mniejszych dawkach gazu można by rzeczywiście używać go do redukowania zużycia paliwa. Ale to tylko takie moje rozważania…
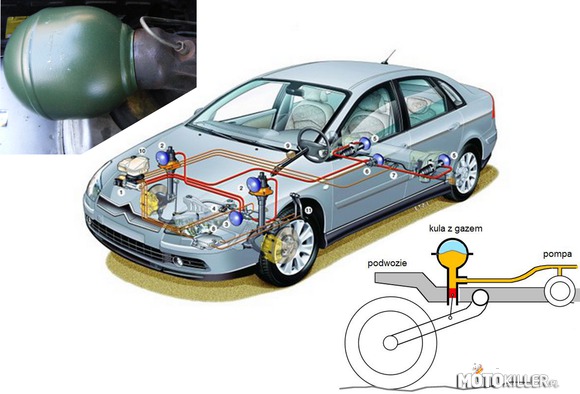
Zaletami dynamicznej regulacji zawieszenia w autach osobowych(z przyczyn oczywistych nie wspominam o autach terenowych) jest możliwość regulacji prześwitu podczas jazdy. Przy małych prędkościach auto stoi wyżej aby samochód bez problemu mógł przejechać np. przez próg zwalniający, natomiast gdy auto jedzie z dużą prędkością po równej asfaltowej drodze może się obniżyć aby do minimum zmniejszyć opór powietrza i zwiększyć aerodynamikę nadwozia.
Jedyną i chyba największa wadą tego rozwiązania są duże koszty przy ewentualnych naprawach. W starszych autach naprawa takiego układu niejednokrotnie przewyższa cenę całego auta. Niemniej jednak dobre układy potrafią wytrzymywać przebiegi około 200 tys. km przy odpowiednim użytkowaniu i konserwacji.
Rozwinę trochę temat samych sfer(zielony element na zdjęciu). Mianowicie mają one kształt(jak sama nazwa wskazuje) kul w których płyn i gaz oddzielone są membraną. To w nich odbywa się sam proces „sprężynowania”. Płyn naciskając na membranę spręża gaz, przez to są one jednym z elementów które ulegają uszkodzeniom.
Opis do schematu:
- Centralka elektrohydrauliczna
- Przednie sfery
- Przedni regulator sztywności
- Czujnik położenia zawieszenia przedniego
- Tylne sfery
- Tylny regulator sztywności
- Czujnik zawieszenia tylnego
- Moduł BSI
- Czujnik położenia koła kierownicy
- Zbiornik płynu hydraulicznego
- Czujnik położenia pedału gazu

Multiair opiera się na mechanizmie wstawionym pomiędzy wałem krzywkowym a trzonem zaworu. Mechanizm składa się z tulejki z zaworem elektrycznie otwieranym, wypełnioną olejem hydraulicznym, z tłokami po obu stronach. Przy zamkniętym zaworze elektrycznym, tłok (górny) napychany przez wał krzywkowy powoduje odpowiednie wypychanie dolnego tłoku za pośrednictwem oleju, popychając również trzon zaworu, otwierając zawór w cylindrze. Zaś otwarty zawór (elektryczny) wypuszcza olej z tulejki, przy czym dolny tłok się nie rusza a zawór w cylindrze się nie otwiera. Zamykanie i otwieranie tego zaworu razem z odpowiednim wałkiem krzywkowym umożliwia więc tworzenie dowolnego profilu otwierania i zamykania zaworów silnikowych oraz ich optymalnego szeregowania.
Przy tym rozwiązaniu, przepustnica już nie jest potrzebna gdyż opóźnienie otwierania lub wczesne zamykanie zaworów ssących, reguluje ilość powietrza wpuszczonego do silnika.
Dzięki tej technologii ciśnienie powietrza w komorze wlotowej jest zawsze jednakowe, co powoduje uzyskanie lepszego momentu obrotowego.
Silnik tłokowy ma zmienne potrzeby oddechowe, które są związane z prędkością obrotową. Przy pierwszym suwie, zawór ssący otwiera się przy górnym martwym punkcie (GMP) i zamyka się przy dolnym martwym punkcie (DMP). Przy wolnych obrotach to zamykanie i otwieranie zaworów staje się blisko GMP i DMP. Przy szybkich obrotach takie szeregowanie powoduje wielkie zmniejszenie ilości ssanego powietrza: tłok próbuje szybciej ssać przez ograniczonej wielkości otwór zaworu ssącego. Przy takich prędkościach, powietrze które zostaje wciągane do cylindra otrzymuje inercję (czy bezwładność) i zmiana szeregowania zaworów ssących do późniejszego zamknięcia - do nawet parę-naście stopni po DMP - umożliwia zassanie większej masy powietrza: powietrze dalej jest wciągane do cylindra, nawet gdy tłok już zaczyna ruszać w górę. Podobnie, pod koniec czwartego suwu, gdy zawór wylotowy się otwiera, inercja gazów wylotowych spowoduje podciśnienie w cylindrze, które może być wykorzystane do wczesnego wciągania świeżego powietrza z kanału dolotowego, zwiększając czas ssania i masę powietrza ssanego.
Silniki MultiAir skutkują zwiększeniem mocy (do 10%), momentu obrotowego (do 15%) przy mniejszym zużyciu paliwa (do 10%) oraz zmniejszeniem ilości emisji spalin (do 10%) w porównaniu z tradycyjnym silnikiem spalinowym. Silnik uporządkowany w system MultiAir płynniej pracuje w niskich temperaturach, ma bardziej płaski profil momentu obrotowego co zapobiega trzęsieniu silnika podczas gaszenia.
Multiair został opatentowany przez firmę Fiat w 2002 r. i wprowadzony na rynek w 2009 r.

W silniku spalinowym Wankla główny element roboczy - tłok - wykonuje ruch obrotowy, podobnie jak w turbinowym silniku spalinowym wirnik turbiny. Jednak zasady działania tych silników są różne. W turbinowych silnikach spalinowych energia kinetyczna rozprężających się gazów działając na łopatki wprawia w ruch obrotowy wirnik silnika. Zasada działania silnika Wankla jest natomiast taka jak tradycyjnego silnika czterosuwowego.
Ciągle tylko silniki w układzie rzędowym albo w układzie V, dla odmiany proszę,,SILNIK WANKLA''
ZASADA DZIAŁANIA:
W tym silniku tłok w kształcie zbliżonym do trójkąta (trójkąt Reuleaux o lekko "wypukłych" bokach), mimośrodowo umieszczony w epitrochoidalnym korpusie, obracając się tworzy komory: ssawną, sprężania, rozprężania (pracy) i wydechową. W zależności od kąta obrotu tłoka komory te zmieniają kształt i objętość. W czasie jednego obrotu wału, silnik wykonuje 3 cykle pracy - ssanie, sprężanie, wydech - silnik dwusuwowy wykonuje w czasie jednego obrotu wału jeden cykl pracy, czterosuwowy zaś na jeden cykl pracy potrzebuje dwóch obrotów wału. W momencie, gdy mieszanka paliwowo-powietrzna jest maksymalnie sprężona następuje zapłon. Mieszanka paliwowo-powietrzna dostarczana jest przez kanał doprowadzający, a spaliny odprowadzane przez kanał odprowadzający. Ruch tłoka jest przenoszony na mimośrodowe odcinki wału centralnego. Ruch rotora jest kształtowany przez koła zębate nieruchomo przymocowane do płaskich ścian komory i współosiowe z wałem centralnym.
To była zasada działania takiego silnika, czas na zastosowanie
ZASTOSOWANIE:
Silnik Wankla po raz pierwszy zastosowano seryjnie w samochodach NSU Spider – prezentacja miała miejsce w roku 1963 na salonie samochodowym we Frankfurcie. Cztery lata później firma Mazda zaprezentowała sportowy samochód Cosmo Sport z pierwszym silnikiem z dwiema komorami wyprodukowanym na licencji NSU-Wankla. W roku 1968 do produkcji wszedł model NSU Ro 80, także z silnikiem dwukomorowym.
Głównymi zaletami silnika Wankla są stosunkowo małe rozmiary i masa, prosta konstrukcja (mniejsza liczba elementów niż w klasycznych silnikach), niewielkie wibracje, niska hałaśliwość podczas pracy oraz osiąganie wysokich prędkości obrotowych i wysoka sprawność mechaniczna. Mimo to jest on stosowany rzadko, zaś wiele prób rozpowszechnienia tego typu silnika zakończyło się niepowodzeniem z powodu problemów konstrukcyjnych i technologicznych. Do produkcji rotorów oraz bloku silnika używano stopów na tyle słabych, że silniki zużywały się dosyć szybko. Główne wady silnika to trudne do uszczelnienia obszary pracy związane z przedmuchami; z tego względu mniejsze jest ciśnienie sprężania i mniejsza sprawność termodynamiczna. Są też większe straty ciepła na skutek bardzo niekorzystnej (szerokiej i płaskiej) komory spalania - co zwiększa straty ciepła i generuje naprężenia termiczne związane z "gorącą" i "zimną" strefą pracy silnika. Nie bez znaczenia jest też spore jednostkowe zużycie paliwa i duża emisja gazów spalinowych na jednostkę mocy. Ta wada, wraz z niedostateczną trwałością uszczelnień tłoka, jest powodem małego zainteresowania tym silnikiem w praktyce motoryzacyjnej. Były nawet sytuacje, gdy bloki silnikowe na skutek naprężeń termicznych nie wytrzymywały i pękały. W praktyce konstrukcja silnika była bardzo trudna do uszczelnienia, a silnik zużywał dużo paliwa.
Wraz z rozwojem techniki firma Mazda pokonała te problemy i zastosowała swój silnik w samochodzie Mazda RX-7. Obecnie już nie produkuje się tego modelu. Zastąpił go nowszy Mazda RX-8. Zastosowany w modelu RX-8 silnik Wankla nazwano Renesis. Kilkakrotnie zdobył on nagrody za najlepszy silnik roku. Konstrukcja silnika jest na tyle uniwersalna, że firma Mazda testuje silnik Wankla – Renesis używający jako paliwa wodoru (RX-8 Hydrogen RE concept car). 22 czerwca 2012 roku Mazda zakończyła produkcję modelu RX-8, który był ostatnim na świecie samochodem z silnikiem Wankla.
‹ pierwsza < 1 2 3 4 5 6 7 > ostatnia ›